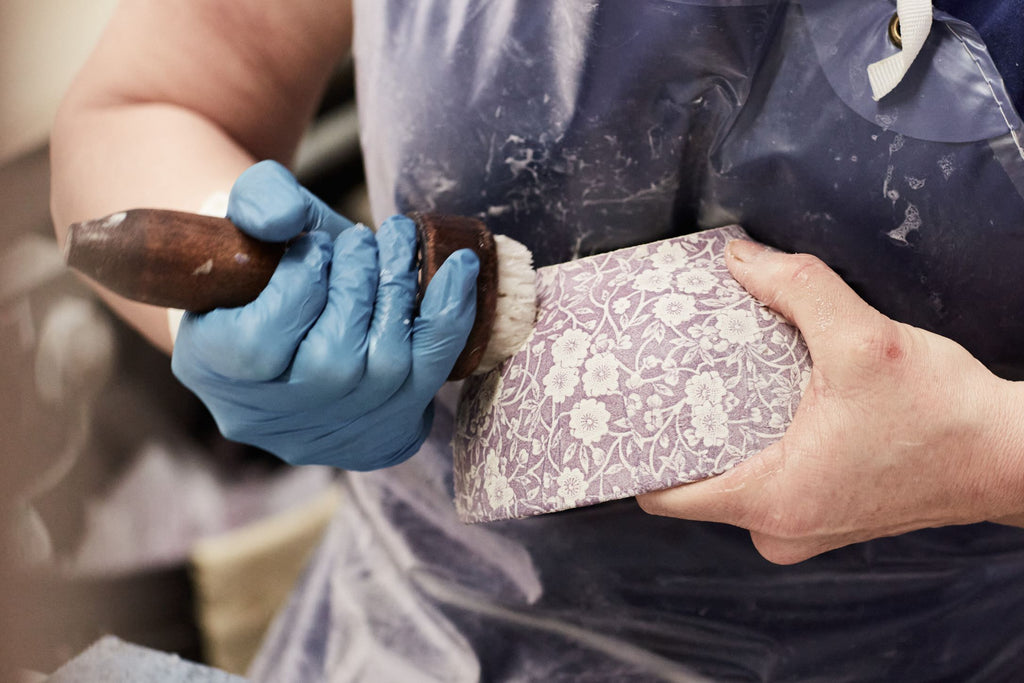
Continuing with our theme of All Made Here, we want to share with you about an integral part of our production process because when we say that every piece of Burleigh has been MADE HERE in the town of Burslem, ‘The Mother Town’, since 1851, we mean it. We are so dedicated to retaining and celebrating our provenance, that we continue to source locally made materials wherever possible, too.
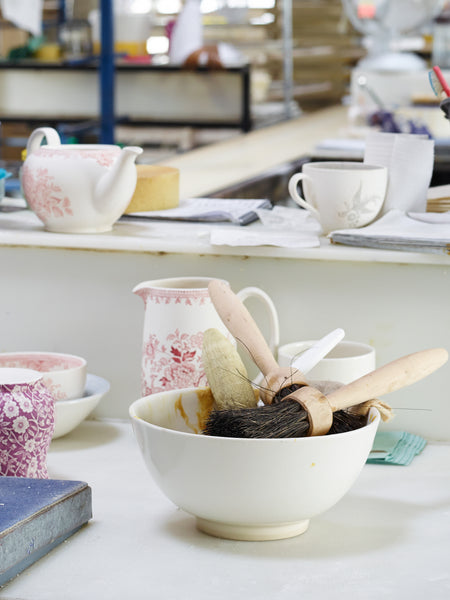
Brushes of various types are used in different departments of an earthenware manufacturer working within a traditional style, like Burleigh. Once the streets of Stoke-on-Trent boasted many craftspeople creating all shapes and sizes of brushes. Turning wooden handles and bristling them by hand; a craft in its own right. When a factory continues the methods used in the area since the 18th century, the brushes remain important.
Biscuit ware at Burleigh is hand brushed, and the entire process of ‘underglaze tissue transfer printing’ hinges on the vigorous brushing carried out after the pattern is applied.

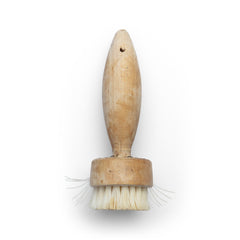
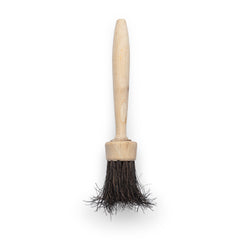
Our tissue paper is specially made to be strong when wet so, as long as the technique of rubbing is correct, the pattern stays intact. Any hard-to-reach areas, like behind a handle, are rubbed with toothbrushes and ‘pegged’ (where a thin wooden stick, much like a lollipop stick, is pushed into the crevices). Once the whole surface has been given this treatment, it is placed onto a slow moving conveyer belt which transports it to the next stage of the process; washing off.
Over time, the brushes wear down so require re-bristling, usually every 6 months depending on use. Eventually after a number of years when the handle is completely worn down, the entire brush would need to be replaced, by our local Brush Maker. Each Transferrer has their own brush, with a wooden handle that slowly moulds itself the shape of the skilled workers hand, rendering them useless to anyone else.

The pottery industry has changed dramatically over the last 60 years, with a decline the number of factories and for those that remain, many chose to modernise. Thus leaving many auxiliary suppliers closing down, due to a general shrinkage of the industry. As well as brush suppliers, paper mills, colour manufacturers, clay mills, engineers, tool makers, plus many more, have gone from hundreds of businesses to a handful. Making life rather difficult for those who genuinely believe the old ways are often the best.
Burleigh utilises the services of S&J Brushes, where Mr Anthony Drosdzowski services all of our brushes, and when needed, creates whole new masterpieces; supporting our craft so that we can continue to celebrate the best of British ceramic design and craft manufacturing.
Brushes are collected from the factory as required and old bristles are removed, then carefully replaced, now using synthetic fibres, or non-animal fibres, rather than the old way of using various types of animal hairs. Carefully knotting in each set of bristles with copper wire.
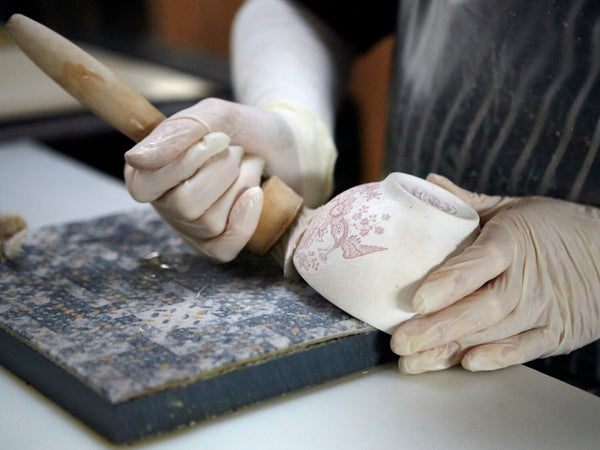
Read more about How We Make Burleigh and browse our collections of handcrafted ware, All Made Here since 1851.
#BurleighPottery